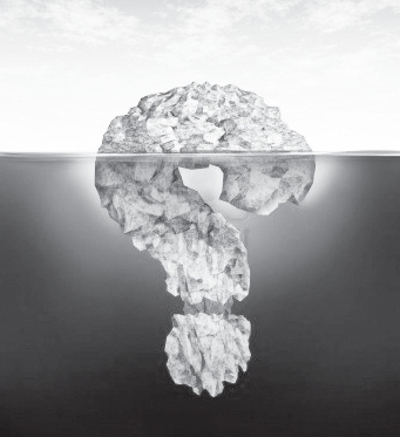
منبع: ماهنامه خانه تاسیسات – شماره ۶ – تیر ماه ۱۳۹۲
استفاده از این مقاله با ذکر منبع مجاز است.
منبع: ماهنامه خانه تاسیسات – شماره ۶ – تیر ماه ۱۳۹۲
استفاده از این مقاله با ذکر منبع مجاز است.
منبع: ماهنامه خانه تاسیسات – شماره ۱۰ – آبان ماه ۱۳۹۲
استفاده از این مقاله با ذکر منبع مجاز است.
منبع: ماهنامه خانه تاسیسات – شماره ۷ – مرداد ماه ۱۳۹۲
استفاده از این مقاله با ذکر منبع مجاز است.
منبع: ماهنامه خانه تاسیسات – شماره ۶ – تیر ماه ۱۳۹۲
استفاده از این مقاله با ذکر منبع مجاز است.
منبع:ماهنامه خانه تاسیسات – شماره ۶ – تیر ماه ۱۳۹۲
استفاده از این مقاله با ذکر منبع مجاز است.
ادامهٔ «یکپارچهسازی سیستمهای هیدرونیک با سیستم گرمایش خورشیدی»
منبع: ماهنامه خانه تاسیسات – شماره ۷ – مرداد ماه ۱۳۹۲
استفاده از این مقاله با ذکر منبع مجاز است.
منبع:ماهنامه خانه تاسیسات – شماره ۷ – مرداد ماه ۱۳۹۲
استفاده از این مقاله با ذکر منبع مجاز است.
منبع:ماهنامه خانه تاسیسات – شماره ۸ – شهریور ماه ۱۳۹۲
استفاده از این مقاله با ذکر منبع مجاز است.
منبع: ماهنامه خانه تاسیسات – شماره ۱۰ – آبان ماه ۱۳۹۲
استفاده از این مقاله با ذکر منبع مجاز است.
منبع: ماهنامه خانه تاسیسات – شماره۱۰ – آبان ماه ۱۳۹۲
استفاده از این مقاله با ذکر منبع مجاز است.
منبع:ماهنامه خانه تاسیسات – شماره ۱۰ – آبان ماه ۱۳۹۲
استفاده از این مقاله با ذکر منبع مجاز است.
منبع:ماهنامه خانه تاسیسات – شماره ۹ – مهر ماه ۱۳۹۲
استفاده از این مقاله با ذکر منبع مجاز است.
منبع: ماهنامه خانه تاسیسات – شماره ۱ – آبان ماه ۱۳۹۲
استفاده از این مقاله با ذکر منبع مجاز است.
منبع: ماهنامه خانه تاسیسات – شماره ۱ – آبان ماه ۱۳۹۱
استفاده از این مقاله با ذکر منبع مجاز است.
منبع: ماهنامه خانه تاسیسات – شماره ۱۰ – آبان ماه ۱۳۹۲
استفاده از این مقاله با ذکر منبع مجاز است.